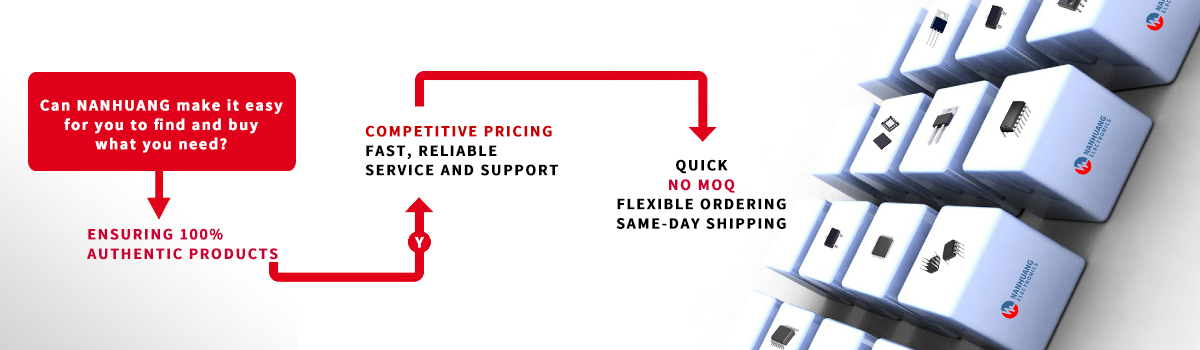
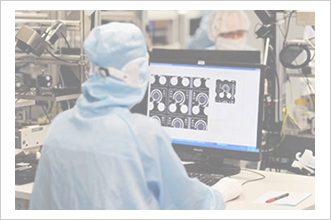
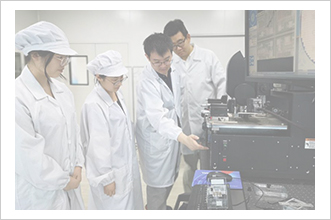

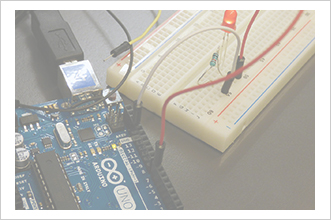
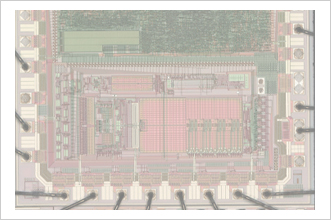
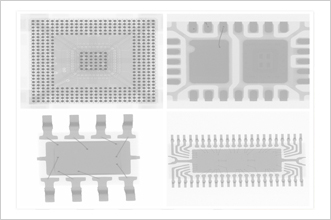
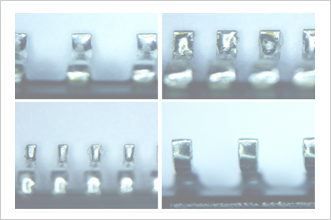

Our team understands the needs of buyers, because we are buyers ourselves, and know that communication, transparency, quality and service are what produce trusting relationships that breed loyalty.
At NHE Electronics, we've been battling the proliferation of counterfeit electronics for over ten years. We know that the existence of counterfeit products is indeed a big problem, and how much time and money counterfeit products waste. As we all know, this problem is not going to go away, but with our vetted supply chain network and advanced lab analysis, we have the experience to navigate complex component sourcing dilemmas.
We have a professional QC team, can monitor and control the quality during the whole process including in-coming, storage, and delivery and etc. All inspections and observations are reviewed by Quality Engineers to evaluate whether we are seeing a new counterfeiting technique or a manufacturing anomaly.
We investigate supplier credit qualification thoroughly, to control the quality since the very beginning. Our suppliers are continuously scored in our business management system and receive feedback ratings for every purchase order processed. This allows our Quality Management System (QMS) Manager to monitor on-time delivery, quality assurance metrics and ERAI/GIDEP notifications, resulting in real-time supplier monitoring.
The first, and most essential, step for any component evaluation is a thorough inspection process. Our high-power microscope provides us with very high-resolution images and depth of field photography, which is very important for our surface and lead detection.
By using industry-proven methods for detecting anomalies of the surface integrity, our inspectors perform a basic scrape test to start, and then swab with mineral spirits, alcohol, or acetone. These basic detection methods check part markings, blacktopping, and mold cavities. Marking permanency and resistance to solvents, resurfacing, dimension verification, marking code matching, high-power magnification inspection of body and terminal condition are standard methods within our inspection process.
X-ray equipment allows us to see the internal structure of the components. This precision equipment can detect 100% of the components on the reel, and compare the internal structure, chip frame, chip size and welding wire position with known samples.
A destructive test that removes the insulation material of the component to reveal the die. The die is then analyzed for markings and architecture to determine traceability and authenticity of the device. Magnification power of up to 1,000x is necessary to identify die markings and surface anamolies.
The spectrometer is used for measuring the controlled elements in lead-free and RoHS compliant devices and determining the composition of plating materials. We also use this equipment for helping to detect reconditioned and resurfaced parts by measuring the plating thickness and variations in the composition of the surface material.
This is not a counterfeit detection method as oxidation occurs naturally; however, it is a significant issue for functionality and is particularly prevalent in hot, humid climates such as Southeast Asia and the southern states in North America. The joint standard J-STD-002 defines the test methods and accept/reject criteria for thru-hole, surface mount, and BGA devices. Devices that are delivered in inappropriate packaging, acceptable packaging but are over one year old, or display contamination on the pins are recommended for solderability testing.
Although the development of new counterfeiting techniques is constantly progressing, so too are the advancements made in our quality assurance program. Since there is no absolute practice, standard, or certification that can prevent fraudulent or counterfeit parts from entering the supply chain with 100% certainty, NHE Electronics imposes strict quality principles that minimize the risk of receiving faulty products in an era of new high-end counterfeiting technologies.
NHE Electronics has been attaching importance to the environmental protection so as to prevent pollution from appearing and satisfy the need for supervision and environmental protection. We will join hands with our Customers,Suppliers,and Government as well as the Community in order to know more about the environmental problem and support the work of optimizing the cooperative partnership, reducing the trade impact on environment as much as possible.
